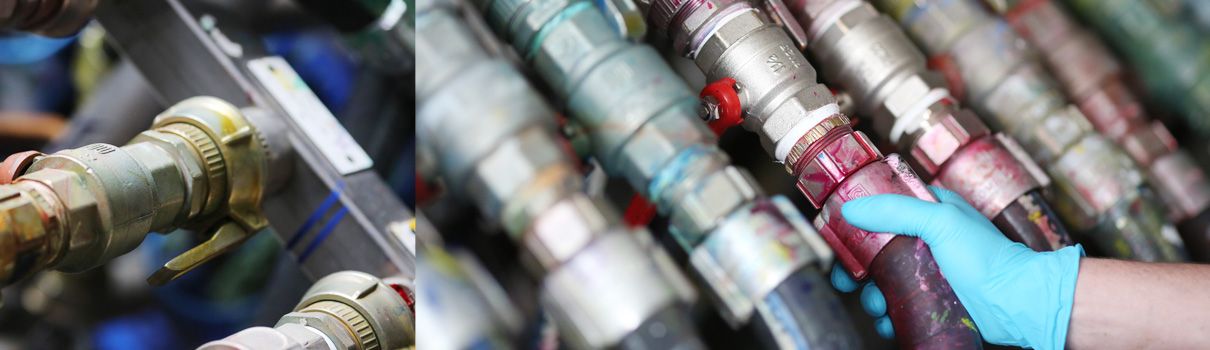
FAQ
What advantages do 2K systems offer?
- higher dosing accuracy when mixing the hardener compared to manual mixing
- therefore consistent quality
- only the quantity needed is mixed or consumed
- no residual quantities, thereby reducing disposal costs
- highly reactive two-component materials with short pot life can be processed
much more easily than with manual mixing - working time savings for the painter, since the removal of the paint/lacquers and of the hardener and,
if necessary, of the dilution is done fully automatically by the 2-component system - display possibility for consumed quantities
- less cleaning effort due to automatic rinsing the plant
Procedure for manual mixing of 2-component paints
- view the technical data sheet of the product to be processed and extract the mixing ratio
by weight and pot life - determine the amount of varnish to be processed while observing the pot life
- thoroughly stir up the container with the base varnish
- determine the required amount of hardener and add it to the master paint,
then mix thoroughly with an electric stirrer for several minutes, also taking into account the bottom and
edge areas of the container - set desired spray viscosity by adding setting dilution depending on the spraying method selected;
please also refer to the technical data sheet of the manufacturer - The paint is now ready for use
What are the advantages of HVLP spray guns?
HVLP (High Volume, Low Pressure, German: high air volume, low pressure) is an internationally recognized low pressure process in painting technology. It is a variant of pneumatic spraying.
When spraying with HVLP paint spray guns, the sprayed material is atomized with a low nozzle internal pressure of 0.7 bar maximum. Here, a material transfer rate of up to 65 % is achieved.
This process reduces the speed difference between material and air flow, resulting in larger droplets and correspondingly less spray mist.
In order to produce an acceptable coating result when painting with HVLP paint spray guns, a higher volume of air is needed to atomize the injection molding material than with high-pressure guns.
The required air volume of 600 to 2,000 L / min can be generated either by a turbine or by a compressor.
HVLP painting is particularly suitable for highly fluid, low-viscosity materials. Even if more compressed air is consumed when painting with HVLP paint spray guns, the saving of the required paint usually outweighs the costs for the higher air consumption.
When painting the HVLP spraying is a slightly higher time than the conventional pneumatic spraying.
The HVLP standard was developed in the US in California and is the strictest environmental law in this regard. The air pressure under the air cap may not exceed 0.7 bar.
What are the advantages and disadvantages of single-coat paints compared to two-coat systems?
To shorten lead times in industrial paint shops, in addition to shortening the drying time, e. g. by using a forced drying, and considerations to reduce the number of steps in painting are made.
If the processor has hitherto worked with a two-coat system consisting of primer and topcoat, it may be considered to omit the primer and to replace the topcoat with a single-coat paint.
The monolayer paint also performs the function of the primer with regard to adhesion to the substrate and corrosion protection. Modern one-coat paints are equipped with zinc phosphate or active corrosion inhibitors to ensure adequate corrosion protection.
These single-coat paints generally achieve the same weather resistance as a two-coat buildup.
The prerequisite is that the previous total layer thickness is maintained.
Decisive for a good function of the one-coat paint is an intensive and consistent surface pre-cleaning, which usually has to be carried out more extensively than when using a primer.
Also of importance is a good part geometry to be coated for a safe application of the required dry film thicknesses.
The time savings in the coating process in comparison One-coat to two-coat system is usually between 20 and 40 %. In addition, the time for drying the primer is saved.
crosshatch
The adhesion of painted surfaces is usually tested by means of a cross-hatch according to DIN EN ISO 2409. Six parallel cuts are made with a cross-cut knife.
The spacing of the cuts is 1 mm for dry film thicknesses of < 60 μm, 2 mm for dry film thicknesses of 60 to 120 μm and moreover 3 mm.
After that, another six incisions are made at right angles, creating a uniform square pattern.
An adhesive tape with a bond strength of 8 to 10 N/25 mm is glued to the resulting square. This is then subtracted with a short jerk at an angle of 60°.
The adhesion is then evaluated by means of a cross-hatch value table. If there is no flaking off, the characteristic value is GT 0.
If more than 65 % of the surface is detached, this means the characteristic value GT 5.
The intersecting cross-cut characteristic values are described and illustrated in the damage classification in DIN EN ISO 2409.
How do I handle mixing 2K paints?
In order to obtain a perfect coating result and the outstanding, good properties of 2-component paints, the following procedure should be taken into account when mixing 2-component paints:
The information on the mixing ratio can be found in the technical data sheet of the manufacturer and must be followed exactly.
Care must be taken to ensure that the weight ratio is relevant when weighing.
When mixing the material in the measuring cup, with volume measuring bars or when processing the material using a 2-component system, the mixing ratio by volume applies.
It may only be mixed as much material as can be processed on a working day. Also, the pot life must be considered; the information on the pot life can be found in the technical data sheet of the manufacturer.
Only after the addition of the hardener, the material may be adjusted to the desired processing viscosity, otherwise the mixing ratio would not be correct and thus the positive properties of a 2-component paint would be lost.
What gloss terms are there and how are they different?
The division of the gloss levels is subject to the new EN ISO 2813.Then there is only the classification
G1 = shiny
G2 = medium gloss
G3 = mat
The previously valid DIN 53778 contains the following gloss designations:
Designation |
Measuring angle/Reflectometer |
|
---|---|---|
high gloss |
20° |
64 [± 5] |
glossy |
60° |
62 [± 5] |
silky-glossy |
60° |
31 [± 5] |
semi-gloss |
85° |
45 [± 3] |
mat |
85° |
7 [± 1] |
In Germany, the following gloss level classification is still used when using the 60 ° ∡ measurement:
dull mat = < 5 %
mat = 5 – 20 %
semi-gloss = 20 – 40 %
silky-glossy = 40 – 60 %
shiny = 70 – 90 %
high gloss = > 90 %
Since these designations are not subject to any standard, the gloss level values are not binding and can only be understood as a rough guideline or customary in the market.
Can 2K mixing plants be rinsed with a VOC-free tool cleaner?
2-component mixing plants, which use solvent-based 2-component PUR systems, can be rinsed with DREISOL TOOL CLEANER VOC-free V0113.
The processing of the cleaner is undiluted. The flushing times should be extended compared to conventional cleaning dilutions.
It is recommended to do this at regular intervals, such as e. g. at the weekend, in addition to rinse with a cleaning dilution.
Due to the low volatility of the tool cleaner, it must be ensured that residues of the cleaner do not get into the 2K materials to be processed, since this leads to a significant drying delay.
DREISOL TOOL CLEANER VOC-free V0113 is a mixture of solvents which, due to its low volatility, is not subject to the 31.
BImSchV (VOC Regulation). This tool cleaner can be distilled by vacuum distillation.
The tool cleaner is not suitable for flushing 2K mixers using 2K epoxy materials.
What is the dew point?
The dew point is a temperature indication.
At the dew point there is a relative humidity of 100 %, as a result of which there is condensation or water precipitation on the boundary surfaces of the substrate. When the dew point is reached, the air is so saturated with moisture that it can not absorb any more water.
Applied coating materials, e. g. as water-based paints, can not give off water and thus the drying is adversely affected. If components from the outdoors are brought into the paint shop and their temperature is below the dew point, water condenses on them. They may only be painted if they have adapted to the room temperature.
What is DIN EN ISO 12944?
DIN EN 12944 deals with the corrosion protection of steel structures by means of coating systems.
This opens up the possibility of choosing exactly what suits the respective requirements from a wide range of different products.
The selection should be based on the following questions:
Where is the object to be coated?
Which loads the coating is exposed to?
What is the useful life of the object?
A distinction is made between different corrosivity categories of C 1 insignificant corrosion load as in heated rooms up to C 5 M (sea) in coastal and offshore areas with high salinity or C 5 I (industrial climate).
What effect does a too low temperature of the coating material have on processing?
A too low temperature in the paint store is noticeable at the latest during processing. The colder a coating material is, the higher its viscosity (thick).
If the material is now adjusted to the processing viscosity by adding solvent, there is a risk of over dilution.
However, this only becomes noticeable after the application, since the coating material is then warmed up by the object or the ambient temperature, the viscosity decreases and the lacquer begins to run.
By a good temperature of the paint storage this source of error can be avoided. Another possibility is to bring the material to processing temperature by means of a preheater at the paint shop.
This technique also helps to save solvents as well. If this is not possible, the material should be stored in a heated room at least 12 hours before processing.
What are high solids?
High solid is a name for high-solids coating materials. In general, the solids content in these systems is over 70 %. Both primers and topcoats can be so declared.
The high-solids coating materials were increasingly developed as part of the VOC guideline in order to reduce emissions through solvent savings.
The processing with existing (conventional) spray technology is usually possible without major investment. Only the system parameters and the spray nozzles are to be matched to the paint material.
The high-solid coating materials of the Dreisol product range bear the abbreviation HS.